lubricating greases: basic concepts
Do you design mechanical components? Do you need to use a lubricating grease to improve the performance of your project? Do you know very little about the characteristics of a lubricating grease? In this article, we will try to clarify the situation, providing you with the basic knowledge on the composition and structure of this type of lubricant, to better orient you in the choice and limit wasted time.
The operation of bearings, gearmotors, chains and mechanical parts in general cannot be separated from the use of lubricating fluids and especially from a targeted choice in harmony with the operating conditions of the component.
To reduce friction and mechanical wear, the choice of lubricant often falls to a lubricating grease rather than an oil due to its intrinsic ability to cling to the friction point during operation.
In the market of lubricants (and of greases in particular), there are solutions that cover a wide range of possibilities when it comes to performance and economics. The purpose of this article is to clarify the three aspects of:
- Chemical composition
- Structural composition
- Criteria for the correct choice of a lubricating grease for industrial applications
1) Chemical composition of lubricating grease
Four main elements can be identified:
Base oil
This element has the most relevant weight in the whole composition. In very fluid greases, it can reach values close to 90%. Its chemical nature significantly affects the performance and economy of the lubricant. The below image highlights the chemical composition of the most common oils used in the formulation, with an indication of the possible temperature range for operation.
Thickener
Also referred to as soap, thickener or texture agent, this provides a fundamental contribution to:
- Adhesiveness
- Filamentation
- Gripping power
- Resistance to washout
- Oil separation
- Drop-point
Organometallic thickeners are distinguished from inorganic ones.
Additives
These are generally used up to a maximum of 4%, ennobling and enhancing application aspects such as:
- Thermo-oxidative stability
- Fluidity at low temperatures
- Protection against metal oxidation
- Anti-wear power
Solid lubricants
Examples are PTFE, molybdenum disulfide (MoS2), graphite, titanium dioxide, boron nitride and so on. These reduce the coefficient of friction locally whilst increasing the protection against mechanical wear. They play a fundamental role by virtue of their high thermal stability at high temperatures, when the conditions around the areas under friction worsen due to exaggerated operating cycles. They represent an emergency lubrication reserve.
2) "Rheological" structure of a lubricating grease
The combination of oil, base, thickener and solid lubricant additives are necessary for the effectiveness of lubricating greases in terms of:
- Material compatibility (plastics and rubbers)
- High-temperature resistance
- Low-temperatures and load resistance capacity
In this guide, we delve into the below aspects.
Equally important is the characterisation of the structure (or rheology), which we can synthetically identify through the following aspects:
- Dynamic viscosity
- Adhesiveness
- Viscoelasticity
- Viscothermal behaviour
Note that the curves shown below were obtained with a precision temperature sensor working in our laboratories, specifically an Anton Paar rheometer model MCR 102 with Peltier hood for accurate temperature control during analyses.
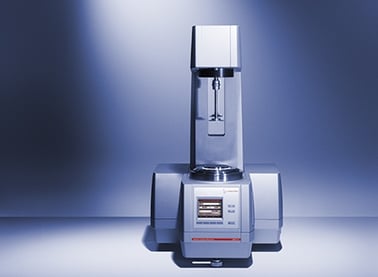
Dynamic viscosity
This is measured in poise (Pa*s), representing the measure of the internal friction of a fluid. For a lubricating grease, this value varies as the amount of stress to which it is subjected varies. The image shows the dynamic viscosity values at a constant temperature of 25° C in a dynamic range between 0.01 and 100 mm/s.
The curves highlight the enormous difference in internal friction existing at low revs compared to higher stresses. The viscosity curves of a grease and a lubricating oil are compared. The latter, rather, shows a viscosity that is substantially unchanged with respect to the shear rate values (stresses). This non-linear behavior of a lubricating grease must be taken into consideration when designing the component, as energy absorption problems could arise at low speeds, especially if an oil was previously used for the same application.
Adhesion of a lubricating grease
This gives an idea of the cohesive power of a lubricating compound, its tendency to "cling" to the point of friction and not to be centrifuged during operations. To quantify the entity, the force required to separate two surfaces is measured between which a 1-mm-thick lubricating film is interposed.
In the image, two curves referring to lubricating greases characterised by different adhesiveness are superimposed. The tests can be repeated on the same sample in order to verify the stability of the cohesive effect of the lubricant after several cycles.
Variation of dynamic viscosity with temperature
The dynamic viscosity value of a lubricating film of a defined thickness (1 mm) at constant stress (1 s-1) is measured by varying the temperature. A characteristic curve of the viscous friction values in the selected thermal range is obtained. The "slope" of the curve is strongly influenced by the choice of the base oil used in the formulation. The use of a stable base oil, such as a silicone (green curve), shows a strong stability with respect to the characteristic curve of a lubricating grease formulated with organic mineral oil (red line).
Consistency
Similar to Shore hardness measured for rubbers and/or Vickers grades for steels, this determines the degree of "softness" of a lubricating compound. Reference is made to the ASTM D-217 standard. Consistency can be:
- Not processed when the measurement is carried out on an "unhandled" test sample for at least 24 hours
- Processed if the test is performed after "manipulation" of the test sample
Penetration value worked < Value penetration not worked
Below is the complete classification of the degrees of hardness of a lubricating grease, with reference to a food product commonly consumed on a daily basis.
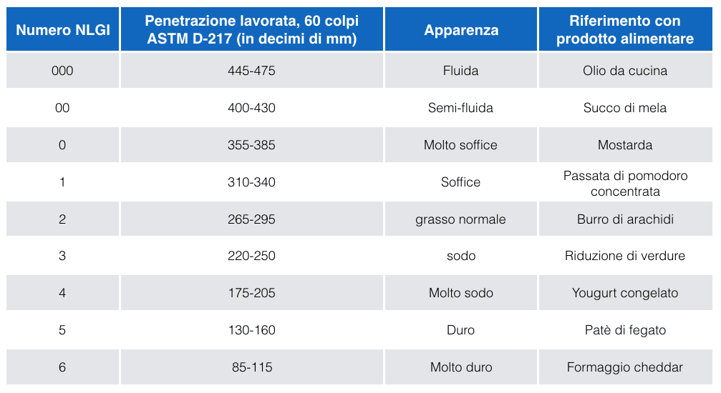
How to choose a lubricating grease
The choice is not so simple! A trained consultant is able to translate the mechanical-dynamic requirements of the mechanical device into a suitable chemical formulation. The right choice starts with a knowledge of the tribosystem, as the set of conditions and variables that affect the immediate surroundings of a friction process. It is very easy to make mistakes. Here, we outline 6 serious mistakes that can be made when choosing a lubricating fluid.
Although the functionality tests allow the designer to experimentally verify in the laboratory and/or in the field the effectiveness of a lubricant solution, it is important to immediately narrow down the field of possible solutions, as certain simulated life tests can last weeks or even months!
Below is a short animation in which the fundamental aspects of a tribosystem are highlighted in terms of:
- Operating parameters
- Interaction parameters
- Tribometric parameters
If you want to find out more about the main factors of industrial lubrication, get in touch with us.