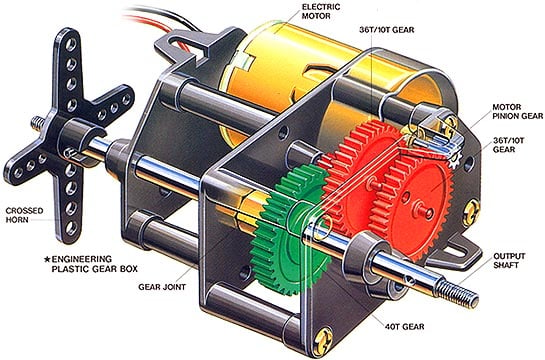
Is your project perfect? Have you started to wonder what might be wrong? Have you ever considered why a mechanical component cannot work without lubrication? Why is its residual life reduced by 95% in the absence of lubrication? And again, why can the right choice of lubricant guarantee smooth operation, longer life and up to 30% better performance? If you think that your mechanical project is okay but you still do not achieve the results you want, continue reading and we will explain the 6 most frequent causes of malfunctions caused by the wrong choice of lubricating fluid. Perhaps you are not factoring in variables of vital importance, such as what is needed to encase and protect surfaces in reciprocal friction and motion, namely a lubricating fluid?
Invest 5 minutes of your time!
We have analysed thousands of mechanical devices – bearings, reducers, hinges, electrical connectors, drive chains, actuators, pneumatic cylinders, pneumatic valves … In doing so, and we realised that:
The lubricating fluid is the most underestimated component during the design phase. Almost always!
The numbers speak for themselves. SKF explains that 36% of bearing failures are caused by inadequate lubrication. And the statistics worsen for components where it is not possible to foresee operations to restore the lubricating film on the points of friction.
For mechanical devices that operate throughout their entire life-span without ever being "re-lubricated", it is advisable to make the right choice to protect yourself from any critical issues that could arise subsequently.
The choice of lubricant is not always so simple. It is necessary to first analyse the operating conditions and the environment in which the lubricating fluid performs its function.
Below, we focus on 6 operating variables that you need to consider in order to avoid premature breakdowns or irregular functioning over time. Bear in mind that, individually or collectively, such factors can threaten the performance of the component you are designing or manufacturing.
1) Ineffective lubrication at low temperatures
A reduction in the operating temperature produces an increase in the internal friction of a lubricant, with the consequent loss of smoothness as you go down the thermal scale. Below are the temperatures at which the main families of lubricating oils (mineral and synthetic) without additives lose their protective power (pour point). Freezing even occurs at below 2/3° C.
Pour point values compared to mineral oil and synthetic oils - Viscosity at 40 ° C - 40cst
Mineral
The increase in friction upon cold start-up causes an increase in the risk of tearing and abrasion of the contact surfaces, with consequent mechanical wear. Repeated cold start-ups could even cause rapid deterioration and malfunctions.
When operating temperatures drop below -10–15° C, it is advisable to evaluate synthetic lubricating solutions.
2) Poor resistance to mechanical loads
One common situation concerns an incorrect evaluation of the load conditions to which the friction surfaces are subjected. When mechanical parts perform their function inside more complex devices (such as pneumatic cylinders in a woodworking machine), it is not always possible to predict the load conditions to which the systems are subjected. A proper design can certainly limit the unexpected but the presence of a lubricating grease with a high load capacity can certainly guarantee an additional protective barrier. Here, we will look at the most important characteristics of a lubricating fluid with a high load capacity and low friction.
OPERATING parameters
- Temperature
- Load
- Sliding speed
TRIBOSYSTEM
BODY
COUNTERBODY
TRIBOMETRIC parameters
- Coefficient of friction
- Mechanical wear
Characterization of a tribosystem
The image shows the 3 macro-areas that characterize a tribological system:
- The operating parameters, that is the operating conditions to which the friction surfaces are subjected
- The interaction parameters, that is the chemical and physical conditions in the immediate vicinity of the contacts between the materials
- The tribometric parameters, the result of the friction process
INTERACTION parameters
- Type of contact and friction
- Type of lubricant film
- Presence of external contaminants
3) Incompatibility of the lubricating fluid with rubbers and plastics
When a lubricating fluid comes into contact with plastic and/or rubber components, it is best to be aware of any interactions in advance. There are highly effective synthetic lubricant chemical families yet equally "reactive" towards certain compounds. In this post, we address the potential incompatibilities between the most common rubbers, NBR, EPDM, FKM, SIL and the most popular lubricating oils.
Also for plastics, it is important to evaluate any embrittlement and/or loss of mechanical properties in contact with lubricants – just think that one of the most commonly-used materials for the production of motorcycle helmets, by virtue of its high impact resistance, is polycarbonate, which tends to "crack" easily when in contact with polar fluids (such as polyalkylene glycol oil).
To establish if any unwanted reactions could occur between plastics and lubricating greases, a specimen of suitably-shaped material is subjected to prolonged mechanical stress with direct contact with the test lubricant. 1000 hours at room temperature with no evidence of cracks or breaks represents a positive compatibility response.
4) Dosing in incorrect quantity on the friction point.
Mechanical parts produced on the assembly line are assembled and lubricated in two ways:
- Manual
- Automatic
If done manually, obviously human error is intrinsic in the operation. For automatic lubrication, it is necessary to ensure that the system controls the quantity in terms of volume dosed, since an excess of lubrication can be as harmful as an insufficient quantity. Trust in an automatic volumetric dispenser, which is more precise than time-pressure varieties, due to being less sensitive to temperature variations around the point of application.
For mechanical parts that require continuous (disposable) lubrication in the maintenance field, also consider the possibility of using an automatic lubricator. In this article, we give you 5 reasons to simplify maintenance operations and keep costs down.
5) Ineffective lubrication at high temperatures
In this page, we have explored the effects of high temperatures on lubricants, the vicious circle that is triggered and how lubricant formulation can be improved through additives and the use of synthetic lubricating oils.
It is important for the designer to know as accurately as possible the temperature range in which the device operates. Above 120° C, the decay phenomena of a mineral lubricating grease can be very rapid and destructive for the mechanical part.
The decay processes of a lubricating fluid are listed in the infographic below. The friction between the surfaces represents a constant, the action of which determines an acceleration of the mechanical wear processes.
friction - heat
Evaporation: loss of mass resulting from the passage of a liquid-gaseous state
Primary oxidation
1st phase of thermal degradation in which a cleavage of the C-C and C-H bonds takes place
Secondary Oxidation
radicalization of the thermo-oxidation process with the formation of carbon deposits
Fluorogrease 935Y
High temperature lubricating grease
High-temperature lubricating grease
100%-synthetic lubricating grease for high temperatures extends the lubrication cycles and life of mechanical parts up to 280° C in continuous operation
6) Does lubricant increase the friction coefficient?
It sounds like a paradox but this can happen! If the lubricating fluid you are using is formulated with high-viscosity base oil and the friction surfaces slide over each other above the critical speed, the same lubricant may brake rather than facilitate sliding. This would result in:
- Increased operating temperatures
- Increased energy absorption
- Contact wear
Lubricating greases for bearings are usually assigned a number, which represents a sort of reference for their potential use under certain dynamic conditions, ergo the speed factor. It relates the bearing dimensions (average diameter dm in mm) and the maximum rotation speed n (in rpm) of the design. The product n*dm refers to a lubricating grease, giving us an immediate indication of its ability to withstand the dynamic conditions of the bearing. The speed factor depends on:
- Base oil viscosity
- Type of thickener
- Consistency (NLGI class) / ratio of the thickened base oil
The table below shows the values of the maximum sustainable speed factors of certain lubricant formulations for rolling bearings.
Type of fat | Base oil viscosity at 40 ° C | Maximum Validity Factor (n * dm) |
Mineral / lithium / MoS | 1000 - 1500 | 50,000 |
Mineral / lithium complex | 400-500 | 200,000 |
Mineral / lithium complex | 150-200 | 400.00 |
Ester / polyurea | 70-100 | 700,000 |
Ester / calcium complex |
15-30 | 1,600,000 |
Ester / polyurea | 15-30 | 2,000,000 |
Getting the right balance between dynamic lubricant viscosity, friction and lubrication is simple for a rolling bearing. Things get complicated when the frictions involve more complex kinematics, where different materials, loads and sliding speeds are mixed, as is the case for the multi-stage gearmotor in the image.
The choice of the lubricant in this case must take into account the load and speed variations along the kinematic chain: high speeds and low loads in the first input stages, high % sliding friction on the wheel-screw coupling, reduced speeds and increasing loads in the final stages.
A thorough analysis by your supplier can help you achieve a noticeable increase in performance in terms of:
- A reduction in energy absorption
- A reduction in mechanical wear and play
- A reduction in wear
- Noise inhibition
WE HAVE A COMMON GOAL, YOURS.
TOGETHER WE WILL FIND THE RIGHT LUBRICANT SOLUTION FOR YOU
GET IN TOUCH WITH US