"Solutions to reduce sliding and rolling friction"
Friction is the force generated by the contact between the surfaces of two bodies that opposes the motion of one towards the other. Different forms of friction can be identified depending on the physical and kinematic conditions that come into play. In this article we will focus on sliding and rolling friction. How do they work? How can the related wear phenomena be avoided?
Sliding and rolling friction are two different forms of friction that can occur depending on certain physical situations and phenomena:
- sliding friction is generated when a body crawls on a surface without rolling
- rolling friction, on the other hand, occurs precisely in the presence of rolling and translation.
In case of sliding and rolling friction, it is recommended to use special synthetic lubricants, the most resistant in all possible friction conditions (tribosystem).
The tribosystem of sliding and rolling friction
As we have just said, the tribosystem is the set of conditions and variables that affect the sliding and rolling friction process, crossing 4 main parameters:
- operating parameters, workload, specific pressures, sliding speed, operating temperature
- interaction parameters, friction conditions (limit, mixed, fluid), presence of process fluids (e.g. powders, acids, bases) and lubricating fluids
- tribotechnical parameters, friction and wear
- friction materials, metals, plastics, elastomers, in relation to the surface roughness of each.
We could give many different examples on types of machinery, operating conditions and suitable lubricants, but the truth is that there are no "general" conditions that are good and useful for everyone. For this reason, before choosing your lubricant, it is essential to analyze together with a specialist the actual conditions in which the tribosystem operates on a daily basis, only in this way can you be sure to develop and use the correct lubricant for your sliding and rolling friction conditions.
Conditions of sliding and rolling friction
Sliding and rolling friction change according to their coefficient of friction, which in turn behaves differently depending on the external conditions and the surfaces in contact.
In order for the lubricant to be able to resist and carry out its work in any operating condition, it is important to monitor and study the coefficient of friction so that it does not exceed its limit condition, that is, the one in which the lubricating film is not sufficient to avoid contact between the surfaces, which instead occurs regularly, producing an inevitable acceleration of the wear processes. In this case it is very important to intervene on the lubricant by adding additives to reduce the friction coefficient.
Only when there is total separation of the contact surfaces can you consider your components safe from any possible damage.
Do you want to deepen your knowledge on anti-friction lubrication? Then read from our Blog Static and dynamic friction: effects on mechanical components.
To find your sliding and rolling friction condition and find the correct lubricant, click below and download our anti-friction lubricants guide for free!
A checklist of the basic requirements of a high load capacity lubricating fluid
Heavy duty lubricants
Complete guide to the key features
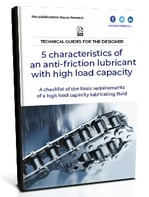
A complete identikit of a lubricating fluid with high load capacity and low friction coefficient