Does an insulating film between the foils of an electrical contact improve durability and operating efficiency? It's hard to believe but it is so! In this article, we tell you how a specially-formulated synthetic lubricating grease can improve the life and performance of electrical switches and connectors.
Electrical connectors lubrication
How to improve durability and performance
Comparison and analysis of the performance of separable electrical connectors: advantages achievable with a correct design and application of a lubricating film
During operation, an electrical connector is subject to:
- Moisture or direct contact with water
- Abrasive wear during insertion
- Oxidation and corrosion
- Contact wear (fretting)
- Thermal changes
These disturbances inevitably lead to a slow and progressive increase in contact resistances with loss of efficiency in signal transmission. A lubricating fluid, however, is an insulator. So how is it possible that the performance of an electrical connection equipped with a lubricating film does not deteriorate but rather improves? To understand this, it is necessary to analyse the morphology of the conductive surfaces in contact under a microscope.
Surface analysis of electrical connectors
The terminal of an electrical connector consists of 3 functional layers: base metal, substrate and coating. Depending on the operating conditions, we can distinguish terminals made of:
- Hard coating
- Ductile coating
Hard coated terminals
Hard coating not deteriorated
Deformation zone with normal contact force
Hard coating: Au, Pd-Ni
HARD SUBSTRATE (Ni - Cu alloys)
BASE METAL
Terminals with ductile coating
Gaps during the insertion
Disintegrated brittle oxide layer
Guaranteed current flow
DUCTILE SUBSTRATE Sn, Sn/Pb
BASE METAL
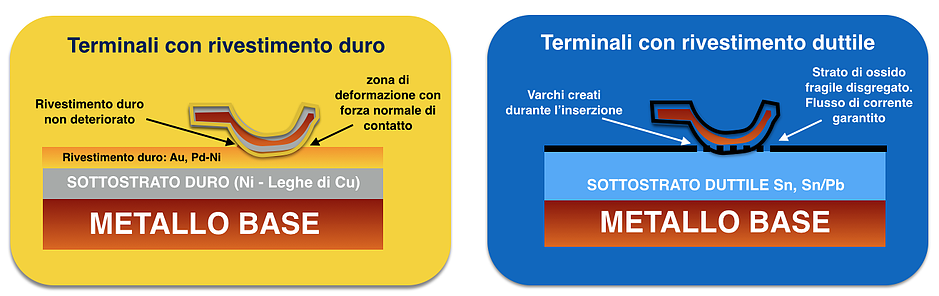
For a hard coating, resistant layer is applied to the substrate generally made of nickel or copper alloys, which does not weaken upon insertion. In the case of a ductile coating, it is the same substrate made of Sn or SnPb alloys, in which oxidizing develops in the overlying coating - a thin non-conductive layer that deforms and disintegrates leaving space for the conductive substrate during the insertion process of the foils. The rupture of the superficial oxide layer therefore represents the necessary condition for the passage of current to take place.
Diagram of the passage of current lines in an electrical connection
Power flow lines
Lubricating grease
Male connector foil
Female connector foil
The image above shows the detail of the contact between the surfaces of two conductive sheets in profile. The passage of current does not take place through the entire available profile but in correspondence with spots or micro-areas. The non-contact areas, shown in blue, are free and thus can be attacked by external agents. These areas could be occupied by a lubricating film, which by virtue of its plasticity would be able to arrange itself in a neutral position and in harmony with the mechanical stresses: vibrations, insertions and so on.
In the image below, rather, two contact plates with and without protective lubricant are compared. On the non-lubricated sheet, the areas represented in green are subject to a process of surface alteration that takes place through well-known phenomena: contact wear and corrosion.
Dry Lubricated
Contact terminal
Current passage area
Insulating area
Lubricant film
Flat view. Comparison between conductive foil with and without protective film: evidence of green areas exposed to atmospheric agents and wear from fretting and abrasives.
Now let's analyse 5 advantages that are obtained by applying a lubricating-protective film on the surfaces of an electrical contact.
1 - Reduction of insertion forces
If not coupled with a sufficient contact force, conductive foils of an electrical connection can cause signal losses or discontinuity in operation following prolonged operation. To limit such undesirable phenomena, manufacturing tolerances are taken during the design phase to ensure that sufficient static friction values and contact forces are guaranteed for correct operation. High contact forces between the foils lead to high insertion forces during coupling, which can cause:
- Wear due to rubbing of surface coatings
- Increased assembly times
- Nuisance to operators during insertion manoeuvres
If properly formulated, a synthetic lubricating grease for electrical connectors can reduce the dynamic friction generated at the moment of insertion, without substantially modifying the static friction, which is instead necessary as seen for electrical continuity.
Insertion friction -> contact wear
2 - Inhibition of fretting corrosion: contact wear
When it comes to the connector of an appliance or one located in the engine compartment of a vehicle, we can be sure of the presence of vibrations. The forced contact between the body and counter-body necessary to guarantee electrical continuity, even if correctly set, does not prevent the triggering of "nano-movements" between the foils, responsible for the well-known phenomenon of fretting wear. It is a form of corrosion that occurs on the contact surface of metallic materials compressed to each other and subject to small vibrations and sliding. The attack morphologically presents itself as pitting or furrows surrounded by the product of corrosion or sometimes merely a loss of lustre of the metallic material.
Mutual movements of connector sheets due to vibrations and mechanical micro stresses responsible for corrosion and fretting wear
Deformation zone with normal contact force
A few nm
3 - Protection from corrosion/oxidation
A lubricating grease for electrical contacts incorporates a package of specific additives for the reduction of oxidation and corrosion. Although some types of oxides are still conductive, preserving the surface from surface reactions is still a considerable advantage. In addition to protecting against the action of humidity, the presence of a lubricating film is able - in the presence of hard gold-based surface coatings for example - to prevent the oxides of the substrate or metal from drawing through the porosities typical of the noble base metal: phenomenon typical of copper and tin alloys.
4 - Stability of the electrical contact resistance
There is a voltage drop at the electrical contact, which is a necessary compromise if you want to have a disconnectable breakpoint in an electrical circuit: the connector. As previously analysed with regard to the morphology of the contact, the surface conductive layers are chosen by virtue of their low electrical resistance to favour the lowest possible voltage drop. Yet, discontinuity is inevitable.
The electrical resistance values that the current flow encounters along its path remain constant:
- After repeated insertions and disconnections
- In the presence of vibrations
5 - Damping the electric arc
This is a somewhat infrequent phenomenon in electrical connectors, whose separation or coupling (plug-in) occurs or should occur in the absence of voltage. Still, it is worth knowing that a lubricating film can significantly contribute to dampening the devastating effects of the electric arc. The electric arc is a rather well-known phenomenon in literature, its extinction depending on the working conditions in low-, medium- or high-voltage, which can be facilitated through various systems:
- Air
- Oil
- SF6 (sulphur hexafluoride)
In the presence of low voltage, such as in domestic electrical switches when a modest-sized arc is generated, air and a precise contact geometry are sufficient. It is known, however, that actuation after actuation, the electric discharges can produce important alterations to the surfaces and generate craters and dissymmetries, causing contact anomalies. The presence of a lubricating grease with a special formulation based on polyethylene glycol or perfluoropolyether can absorb the energy of the electric discharge without carbonising or leaving solid deposits harmful to electrical continuity.
We have listed some advantages that a lubricating fluid can contribute to generate in an electrical connector in operation, in the guide below, we will compare how the electrical contact resistance and wear index parameters change according to the number of insertion and disconnection cycles to which they are subjected, the operating time and the presence or absence of protective lubricating film. We start from the characteristics of a conductive foil, addressing the following aspects:
- Surface stratigraphy
- Contact electrical resistance
- Surface wear phenomena
- Measures to improve the contact qualities
- Characteristics of a good lubricant formulation for electrical contacts
Electrical connectors lubrication
How to improve durability and performance
Comparison and analysis of the performance of separable electrical connectors: advantages achievable with a correct design and application of a lubricating film