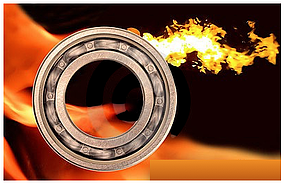
In this article we will analyze 9 benefits that a lubricating fluid can bring to a mechanical device, when it is formulated:
- with synthetic base oils
- to work at high temperature
- Evaporation
- Primary oxidation
- Secondary oxidation
We will provide 9 valid reasons to design your electromechanical device bearing in mind a lubricating fluid that has what it takes to withstand prolonged periods of operation at high temperatures.
(1) - Why the upper operating temperature of a mechanical device is not always certain
theoretical temperature of the project
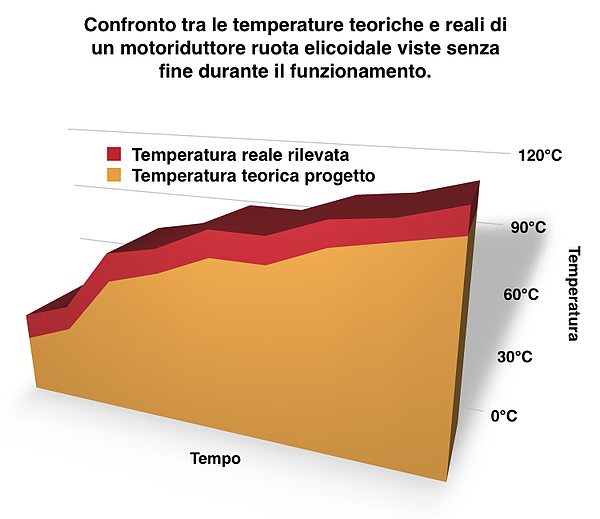
(2) - Why antioxidant additives can help keep the lubricating film active
A lubricating film in operation can reach very small dimensions (1/20 of the diameter of the human hair), especially when temperatures exceed 100-120 ° C. The presence of specific additives for high temperatures can significantly delay the beginning of secondary oxidation, and keep the lubricating film active much longer.
(3) - Why the separation of the friction surfaces is optimal if the film is hydrodynamic and not dry!
There are no optimal operating conditions if two surfaces in friction and in the presence of a load are dry lubricated!! Solid lubricants: graphite, PTFE, boron nitride, molybdenum disulfide, can contribute to lubrication or provide emergency help when the fluid film is absent, but cannot last long in the absence of an active and reactive "fluid" film between the surfaces in friction. As when using a PTFE grease or a Teflon grease, the presence of the solid lubricating additive (PTFE) certainly cannot replace the effectiveness of the base oil. Additives help improve lubrication conditions, but certainly cannot replace them.
Above: Hydrodynamic lubrication
Below: Lubricant film present and active
(4) - Why a layer of charred grease between two frictional surfaces doesn't help!!!
The image below compares 2 lubricating greases subjected to the same test conditions, 24 h at 150 ° C. The image shows:
- (A) a lubricating grease formulated for high temperatures with synthetic oil, and lithium soap.
- (B) a generic lubricating grease formulated with mineral oil and NLGI 2 lithium soap.
Grease B's non-existent lubricating power is very clear: formulated with mineral oil, it is by now deprived of a considerable part of base oil and completely carbonized.
Testing in the oven 24h at 150 ° C
(5) - To limit mechanical wear from friction
Two metal surfaces, if suitably separated and already subjected to running-in, have no reason to lose material, that is, to undergo mechanical wear from friction. The thinning of the lubricating film at high temperatures reduces the lubrication meatus and increases the possibility of contact between the surfaces. A synthetic base oil has a more stable viscosity as the temperature changes and it is therefore possible to exploit this intrinsic advantage and use more viscous oils, which allow for a more effective separation of the friction surfaces.
(6) - Why mineral oils evaporate more easily
A lubricating fluid, grease, oil or paste, is always composed of a base oil, present in the formulation in a minimum weight of 60-65% up to 99% and more. A mineral oil has little chance of surviving when compared with a synthetic oil, just look at the loss by evaporation according to Noack!
If the tribosystem (lubrication point) does not include any cycles to restore the lubricating film, it's done! Once the most consistent part, responsible for the separation of the friction surfaces has been lost by evaporation, a dangerous vicious circle will begin:
- Thinning of the lubricating film
- Mechanical wear
- Abnormal increase in the friction coefficient
- Loss of efficiency
- Increased noise
- Premature blocking of the device
(7) - Why there is no need to relubricate the friction surfaces
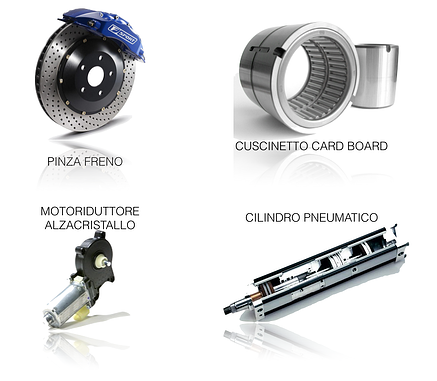
(8) - Why a synthetic grease performs at low temperatures
Comparison of lubricating base oil temperatures
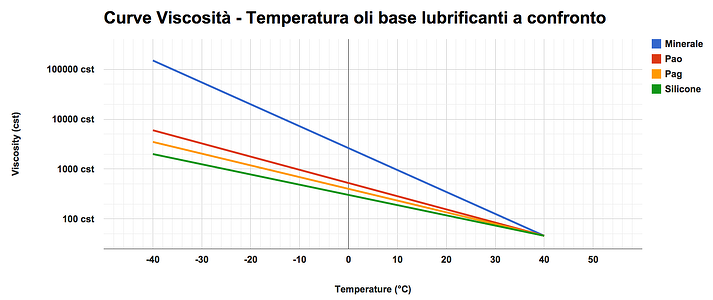
(9) - Why the cost / benefit ratio is often favorable
That's right! A lubricating fluid formulated with synthetic base oil costs more than one formulated with mineral base oil. But what matters is the comprehensive income statement which is obtained through an accurate analysis of all the benefits deriving from an improved and customized formulation for use at high temperatures:
- extended lubrication cycles = reduced product use and lower maintenance costs
- low evaporation = reduced product use
- greater compatibility with plastic materials = greater reliability of the lubricated component and lower returns
- delayed primary oxidation = greater thermo-oxidative stability
- greater persistence on the friction point = reduced maintenance costs
In this article we have seen some of the benefits that can be obtained in terms of efficiency and durability of mechanical devices if synthetic lubricating oils are used instead of mineral oils, and if lubricating greases for high temperatures are used instead of standard lubricating greases formulated for general purposes.
The life span of an electromechanical device is influenced by numerous factors:
- Choice of materials
- Manufacturing tolerances
- Production methods
- Checks on finished pieces
- etc.etc
The correct selection of the lubricating fluid to be included in the mechanical devices is often underestimated in the design phase, but as we have shown it can contribute to considerably increase the performance of a mechanical device, especially in the absence of a stage to restore the lubricating film (maintenance / relubrication cycle).