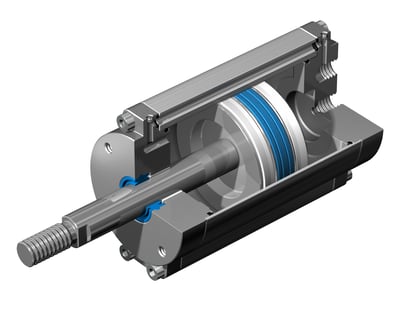
1 - High viscosity temperature coefficient
2 - High thermo-oxidative stability
One aspect of primary importance is the resistance of a silicone grease to heat. Although evaporation processes occur even at lower temperatures and for lighter fractions, even at around 130°–150° C, the most important factor in a silicone grease is its ability to delay the phenomena of primary and secondary oxidation, which represent crucial phases in the destructive process of the lubricating film. Silicone fluids in continuous operation can guarantee regular operation when there is a hydrodynamic film on the friction surfaces, resisting temperatures up to 180°–200° C.
3 - Low coefficient of friction
Silicones are "slippery" by nature. This is due to the particular structure of the siloxane polymer, characterised by wide bond angles between silicon and oxygen that determine one of the main properties of the lubricating grease in which it is contained: the static and dynamic coefficient of friction content. This property is much more evident in the presence of friction between elastomeric surfaces, such as in rubber seals and seal rings sliding on plastic.
4 - Compatibility with plastics and elastomers
A silicone grease tends to be inert towards plastics and elastomers, thus it does not produce substantial structural variations in terms of volume, weight, tensile strength or hardness. For this reason, it is used as an adjuvant in the assembly of rubber seals (EPDM seals) and as a lubricant in operations with various mixed couplings: metal/rubber, metal/plastic, rubber/plastic ...
5 - Good noise damping effect
"Noise" generated during the operation of a kinematics can have a range of sources and levels of acceptance that depend on subjective parameters. It has been experimentally proven that the greater the thickness of the lubricating film, the more effective the barrier interposed between the potentially noise-generating parts in friction. By virtue of the high viscosity index described in Point 1 and therefore of the possibility of being functional and remaining in a fluid state even at lower temperatures, a silicone grease can be formulated with oils of higher viscosity than other types of synthetic lubricating greases and ergo, perform lubricant and anti-noise functions more effectively. Indeed, a silicone oil with a viscosity of 100,000 cst at 25° C can be used up to temperatures of -40° C, which would be impossible for a lubricating oil of any other chemical nature, even synthetic.
6 - Water repellent
A silicone lubricating grease is insoluble in water, making it preferable for use in numerous applications with potential contact with polar fluids intercepted by the lubricated device.
Despite the unrivalled characteristics that a silicone grease possesses compared to other synthetic lubricating greases, there are some weaknesses that must be taken into consideration in the design phase:
- Poor load resistance capacity – in the presence of high frictional force and metallic surfaces in friction, silicone lubricants easily lose their lubricating power
- Incompatibility with painting processes – the presence of silicone during the deposition of paints can cause irregular adhesion and the formation of inhomogeneity
- Difficulty to improve the basic properties with additives, since additives are not soluble in silicone fluids across the broad range of temperatures by which they are distinguished
- Low resistance to shear stresses
- Incompatibility with electrical functionality – migration of volatile fractions in the conductive areas of electrical signal switches (low current), with risk of signal fragmentation
7 - Hybrid silicone formulations: a new frontier in lubrication
As mentioned in the introduction, some industrial sectors (such as the automotive) do not look favourably on the use of silicones in the mechanical devices that comprise a vehicle. Although many components, such as flexible remote controls and some braking system parts, are notoriously coated in silicone lubricating solutions, the “silicone free” limitation remains, mainly due to Points B and E described in the previous paragraph. Yet, the chemistry of lubrication is evolving. Silicone greases and fluids have been developed that significantly compensate for the "deficiencies" described prior, thanks to the coexistence of functional organic groups, namely hybrid formulations.
In this article, we have listed the properties of a silicone lubricating grease and the reasons for its increasing use in the most diverse industrial sectors.